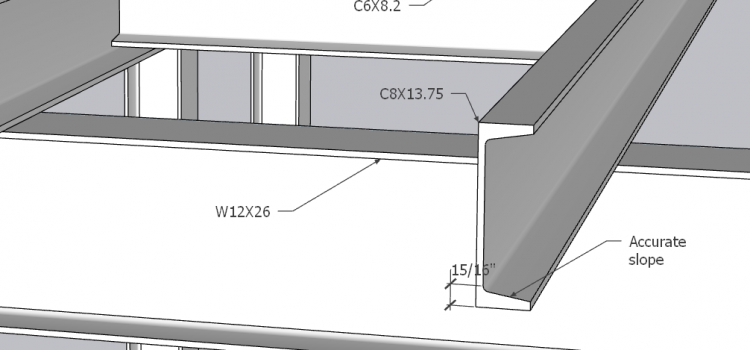
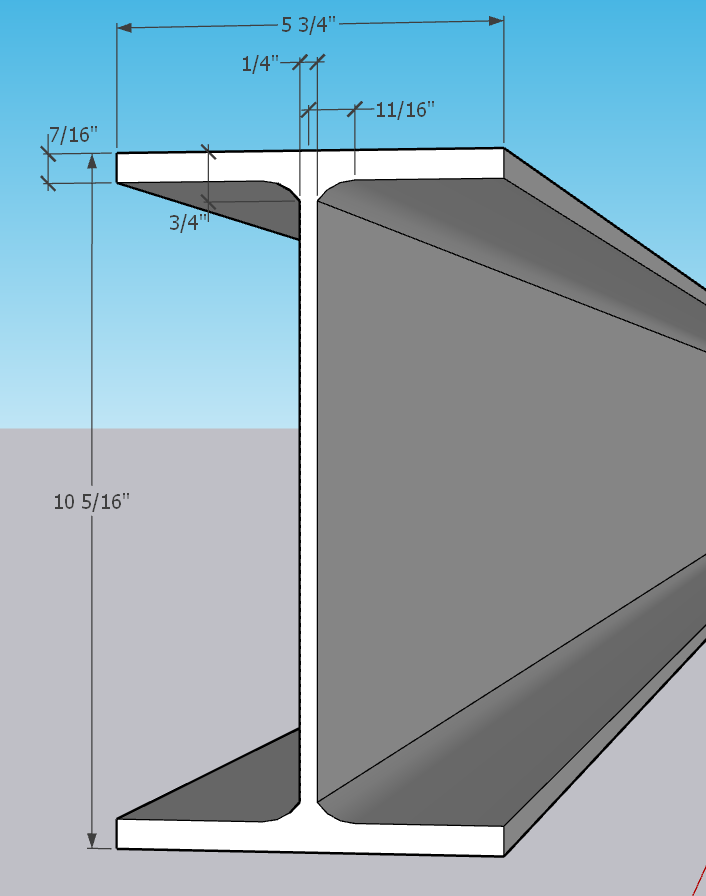
Steel design software without accurate structural profile shapes is pretty much useless. It’s not enough for an AISC W10x26 beam profile to match the nominal height and width of 10 and 6 inches respectively.
For accurate design and connection detailing, we needed to take it a step further and develop a tool for importing an entire database of standard steel profiles into SketchUp while taking into account the profile area, weight, flange thickness, web thickness, k, and k1 values.
One of the first tasks we worked on was to create a Structural Shape Importer. I’m not sure yet whether this tool will be ‘internal only’ or if it will become part of the public version of DECAsteel, but it allows us to import accurate structural profiles into DECAsteel from any source / standard whether from CISC, AISC, British, Australia, German, Chinese, it doesn’t matter.
The only requirement is that the key properties of the shape are saved in an Excel spreadsheet. Here’s how it works:
- Select your database Excel file
- Choose the shape type you want to import (C, L, I, S, Tube)
- Map the key shape properties to the columns in the spreadsheet
- Click the import button
In a few seconds, the DECAsteel shape library will be imported and ready to use to create beams, columns, and bracing and you never need to question the accuracy as long as the original Excel file was created by a reliable source.
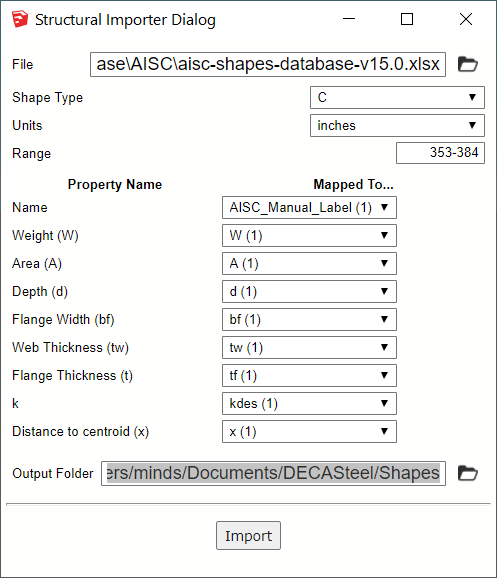
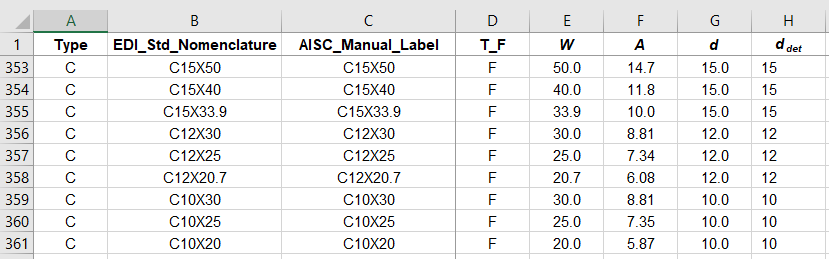
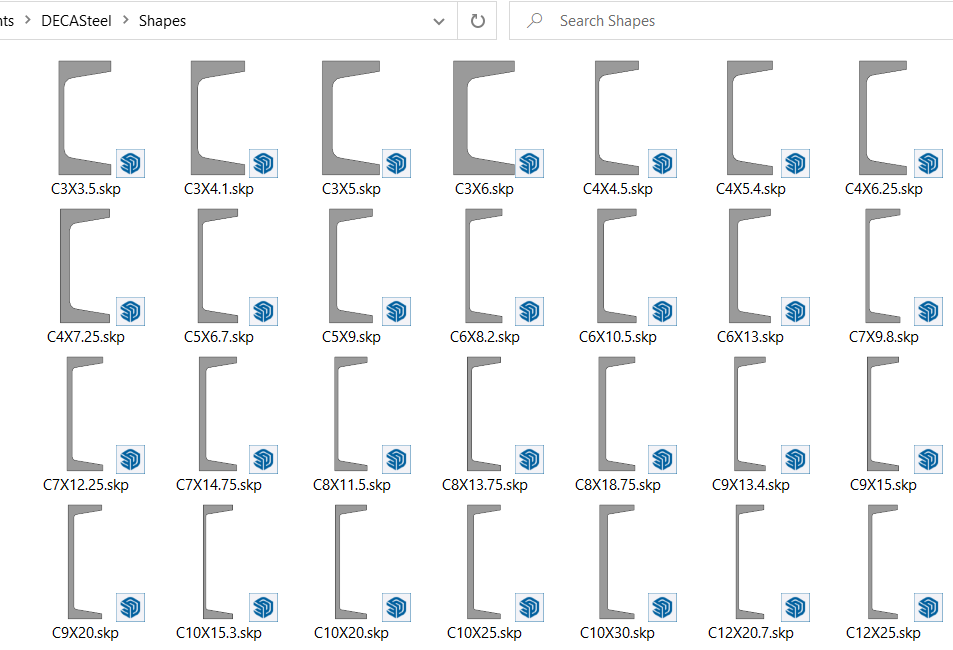
With the shapes imported, I can now use them to model my structure and detail the connections using DECAsteel.
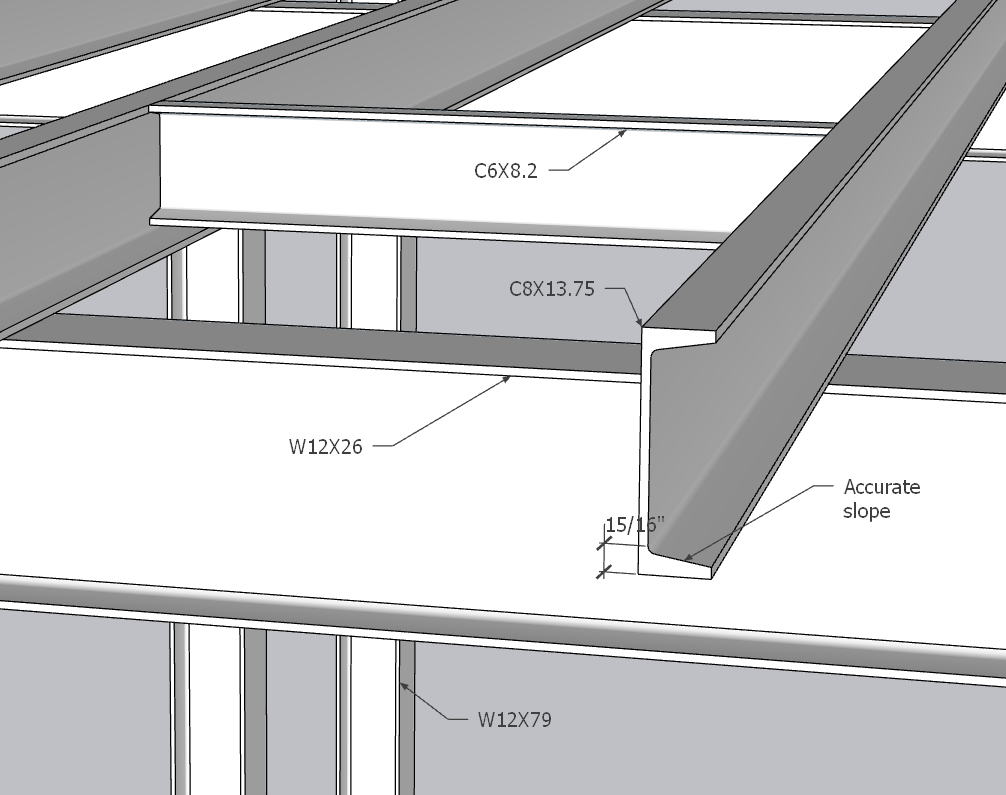
There are a few challenges still remaining for us:
- Tracking down and obtaining permission from various design authorities throughout the world to utilize their database with our software
- Determining if there are more key properties that should be imported besides the ones shown above
- Determining if it is important to maintain a consistent root radius when dealing with k and k1 values. It seems that radii can vary depending on the steel manufacturer so the actual radius value appears to be not a critical design element.
- For C-shapes, the database gives the average flange thickness how is this actually calculated? Is it based on the standard bolt gage location? Or is it based on mid-way between the inside face of the web and tip of the flange? Or maybe something else?
If you have any insight into the items above or have any other feedback about this topic, we’d love to hear from you. Please leave a comment below or start a discussion in our Community Forum.